后张法预制箱梁施工中常见问题及解决方法
浏览 发布时间 2015-5-13 14:32:07
1· 后张法预制箱梁定义
后张梁是在台座上绑扎钢筋制模,按设计预留孔道,将锚具固定好,灌注砼,当砼强度达到设计强度的80%时,将钢绞线或钢丝束按设计的数量穿入预留孔道后用千斤顶进行对称张拉、封锚将应力永久性存入梁的主体。下面就后张砼梁的预制技术、施工工艺,综合现场施工经验,发表笔者的见解。
2· 后张梁施工中常见的问题
①腹板、锚垫板后面砼浇筑不实造成张拉时砼局部压碎,甚至锚垫板压碎。②带角度预制梁在张拉过程中出现梁端小角度部分拉裂现象。③预留孔道在施工过程中漏浆,无法张拉,需要清孔。④预制梁存放时间长上拱值过大。⑤粱顶面砼表面细小裂纹。
3· 针对以上提出的问题结合某桥新建工程笔者的个人看法
某桥新建工程:某桥上跨客运专线和既有铁路线、快速公路。公铁立交部分孔跨(12 号~16 号墩),共1 联。既有线铁路和预留二线位于第14 跨中间,既有铁路距离14 号墩垂直距离7.24m,预留二线距离13 号墩垂直距离5.9m;客专位于第15 跨,客专右线距离15 号墩垂直距离5.8m。本桥跨径为:4*35;上部结构采用预应力砼(后张)简支小箱梁,桥面连续;全长140m。
施工时具体措施如下:
3.1 由于腹板厚度薄,与底板成一定角度且预应力管道约占腹板厚度一半,易产生振捣不密实,出现蜂窝现象。为解决锚垫板后面砼浇筑不实造成张拉时砼局部压碎,甚至锚垫板压碎。在施工中根据钢筋的疏密程度,采用砼配合比粗骨料两级配的方案,碎石粒径0.5~1cm30%、1~2cm70%,充分增强了砼和易性及密实度。对砼拌合材料的误差进行控制:在误差方面,水、水泥、外加剂和干燥状态下的掺合料秤量应控制在±1%,对于粗、细骨料需要控制在±2%;投料顺序:按照细骨料、水泥、掺合料、高效减水剂的顺序投入混合料,并搅拌30s,然后加水搅拌30s,最后加入粗骨料搅拌60s,卸料;搅拌时间控制在120s~180s,砼搅拌到各种材料混合均匀,石子表面包满砂浆,并且颜色保持一致,每个投料阶段不应少于30s。采用附着式振捣器配合20 振捣棒进行振捣,控制砼的捣固时间、插捣间距,将砼内气体引出,灌注砼时既不能过捣也不能漏捣。严格按配合比施工。为防止粘模,采用模板漆作脱模剂,保证了砼表面的光滑度。采取以上措施避免了砼表面蜂窝麻面,解决了锚垫板后面砼浇筑不实现象。
3.2 为避免带角度预制梁在张拉过程中出现梁端小角度部分拉裂现象,加强小角度部分砼捣固、适当增加钢筋数量方法解决。一旦出现拉裂现象,采用环氧树脂、乙二胺、二丁脂、丙酮、砂处理,比例为:配合比10:1:1:2进行修补后,再采用黑白水泥按照试验比例(2:1)进行抹面,保证砼强度和外观颜色一致。环氧砂浆配制工艺:环氧树脂加热至60℃,加入二丁脂和丙酮拌匀,加入乙二胺拌匀,再将预热至30℃的填充料加入拌匀。
3.3 预留孔道在施工过程中漏浆,无法张拉,需要清孔。施工中采用比波纹管直径略小的塑料管与波纹管同时预埋,待砼达到80%后,将塑料管拔除,避免砼进入波纹管,造成堵塞,影响穿束。
3.4 由于征拆影响,桥下部结构无法施工,且因客专开通工期要求,必须先施工预制梁,导致预制梁在场地存放时间较长,必须采用堆载方式减少预制梁上拱。根据桥铺砼重量及预制梁顶平面面积,平均分配到每片预制梁重量进行计算,得出每片梁应承担的力。计算重量后,采用砼块堆载,在每块砼下放置连续梁施工所剩木方进行分荷的方法(如表1所示)。
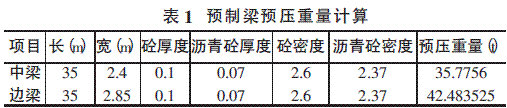
①箱梁徐变上拱监测。对梁体两端支座位置及跨中采用精密水准仪配合精密水准尺进行抄平监测。通过计算进一步确定梁体的上拱,通常情况下,上拱值=两端读数值之和/2-跨中读数值。安排专人同时配备专用仪器进行监测,桥梁架设后,在靠近支座选择确定两端测量位置。
②箱梁徐变上拱控制。
1)对水灰比和水泥用量进行控制:水灰比和水泥用量作为影响徐变上拱的重要因素,通常情况下,当水灰比相同时,随水泥用量增多徐变变形逐渐变大;当水泥用量一定时,随水灰比的增大,徐变逐渐增加。因此,在施工过程中,需要对配合比进行严格的控制,选用的水泥用量和水灰比尽可能小。
2)选择骨料:在砼中,骨料的作用主要是约束水泥浆体的徐变,骨料的弹性模量和体积含量等因素决定着约束的程度,为了进一步控制砼的徐变变形,在施工过程中,选用的石灰石碎石骨料的弹性模量尽量高。
3)砼养护:通过对砼进行洒水养护,进而在一定程度上充分确保梁体的表面湿润性,进一步延长养护时间。
4)对终张拉时间进行控制:对于徐变上拱来说,根据线性徐变理论,施加预应力时梁体的弹性上拱量决定着徐变大小,通常情况下,较低的弹性模量造成的徐变上拱比较大。在这种情况下,需要对预应力张拉时间进行严格的控制,当砼强度及弹性模量符合设计要求后,再进行相应的终张拉。
5)控制张拉工艺:为了防止超张拉,进一步满足预应力徐变上拱限值的要求,需要实测预应力筋的管道摩阻,同时修正张拉应力,并施加预应力。
3.5 预制梁梁面施工时,采用橡胶锤对砼面进行3 次敲击后再进行收浆抹面,防止了砼表面细小裂纹的产生,既保证了工程质量,又解决了美观问题。
3.6 预应力施工注意事项:
①下料、穿束。利用砂轮锯切断钢绞线,同时用铁丝绑扎切割口两侧30mm 处;按照实际计算长度加100mm 余量确定下料长度;按编号分类存放钢束,搬运时支点距离控制在3m,端部悬出长度控制在1.5m。在穿束钢绞线束时,需要对孔道内的杂物进行清除处理,在待穿孔道的一端设置卷扬机,将钢丝绳利用钢丝引入孔中,并拉至另一端,穿束后需要尽快进行张拉处理。
②张拉设备及仪表。定期维护和校验张拉所用的机具设备及仪表。在下列情况下,必须对张拉千斤顶进行重新校验:张拉次数超过200 次;校正期限超过1 个月;千斤顶经过修理。油压表的精度为1.0~0.4 级,读数不大于1MPa,防振型。根据管道磨阻试验、油顶与油表检测书中公式进行计算得出实际油表读数。
③控制张拉力:
1)按照设计规定对锚下张拉控制力进行处理。2)预应力筋张拉控制力:
a.计入锚圈口摩阻损失。
b. 修正孔道摩阻损失,在张拉过程中进行调整。
c. 最大张拉控制力和规范规定值在任何情况下不得超过设计规定值。
④校核预应力筋张拉力:
采用张拉力控制预应力筋,同时以伸长值进行校核。实际伸长值与理论伸长值之间的差值控制在6%以内,否则需要暂停张拉,查明原因并采取措施进行调整,然后进行张拉。
1)采用设计值处理理论伸长值。
2)在初应力后开始量测实际伸长值ΔL,伸长值ΔL2根据量得的伸长值ΔL1 加上初应力下进行推算,即ΔL=ΔL1+ΔL2。
a.对于初应力,通常情况下,需要根据力筋长度、弯曲程度可取张拉控制应力的10%~15%。
b.推算伸长值ΔL2 :对于力筋来说,由于松紧、弯曲程度不一致,在初应力以下拉伸过程中,一方面有弹性伸长,另一方面有非弹性伸长,在这种情况下,不宜采用量测方法。
3)判断超误差的原因及采取的措施。
对于伸长值来说,过大或过小都会对预应力砼结构产生影响,通常情况下,产生超误差的原因主要包括:
a.作业人员在进行量测、读数时,存在的误差;
b.千斤项、油表故障;
c.千斤顶、油表未校验或校验过期、使用次数超过规定;
d.垫板与孔道不垂直或管道局部有灰浆;
e.孔道的摩擦损失计算与实际不符;
f.力筋材料质量不稳定;
g.力筋弹性模量与计算时的取值不一致;
h.操作方法不当,两端伸长值相差过大。
⑤断丝、滑移限制。按照施工规范要求,控制断丝、滑移量。通常情况下,出现断丝、滑移的原因主要包括:锚具、夹具、钢丝沾有油污;锚具不良;锚具与孔道不垂直;力筋材质出现问题。
⑥补偿预应力筋回缩产生的预应力损失。在施工规范容许值内控制预应力筋回缩。当回缩值比较大,并且长度较小时,在这种情况下,会对预应力筋的锚固性能产生影响,需要给予补偿。产生回缩的原因包括:锚具、夹具、钢丝沾有油污;锚具不良等。
⑦紧急处理锚固区发生的裂纹。对于锚固区来说,如果发生局部裂纹,在这种情况下,必须停止一切张拉和砼作业,查明原因并提出处理措施,然后才能复工。裂纹发生的原因主要包括:砼强度不足、加强钢筋设置不当、张拉力过大等。
⑧压浆封锚。完成终张拉后,在48h 内进行管道压浆处理。压浆时和压浆后的3d 内,梁体及环境温度不低于5℃。浆体水胶比不应超过0.34,水泥浆不得泌水,0.14MPa 压力下泌水率不得大于2.5% ;压入管道的浆体不得含未搅匀的水泥团块,终凝时间不宜大于12h。
4· 结论
后张法预应力砼箱梁的预制,经过施工技术的改进,最终解决了预制箱梁腹板、锚垫板后面砼浇筑不实、带角度预制梁在张拉过程中出现梁端小角度部分拉裂、预留孔道在施工过程中漏浆、上拱值过大、粱顶面砼表面细小裂纹、内膜拆模困难等影响预制构件质量的各种现象,最终预制的箱梁棱角分明,线条顺适,色泽一致,真正做到了内优外美。
后张梁是在台座上绑扎钢筋制模,按设计预留孔道,将锚具固定好,灌注砼,当砼强度达到设计强度的80%时,将钢绞线或钢丝束按设计的数量穿入预留孔道后用千斤顶进行对称张拉、封锚将应力永久性存入梁的主体。下面就后张砼梁的预制技术、施工工艺,综合现场施工经验,发表笔者的见解。
2· 后张梁施工中常见的问题
①腹板、锚垫板后面砼浇筑不实造成张拉时砼局部压碎,甚至锚垫板压碎。②带角度预制梁在张拉过程中出现梁端小角度部分拉裂现象。③预留孔道在施工过程中漏浆,无法张拉,需要清孔。④预制梁存放时间长上拱值过大。⑤粱顶面砼表面细小裂纹。
3· 针对以上提出的问题结合某桥新建工程笔者的个人看法
某桥新建工程:某桥上跨客运专线和既有铁路线、快速公路。公铁立交部分孔跨(12 号~16 号墩),共1 联。既有线铁路和预留二线位于第14 跨中间,既有铁路距离14 号墩垂直距离7.24m,预留二线距离13 号墩垂直距离5.9m;客专位于第15 跨,客专右线距离15 号墩垂直距离5.8m。本桥跨径为:4*35;上部结构采用预应力砼(后张)简支小箱梁,桥面连续;全长140m。
施工时具体措施如下:
3.1 由于腹板厚度薄,与底板成一定角度且预应力管道约占腹板厚度一半,易产生振捣不密实,出现蜂窝现象。为解决锚垫板后面砼浇筑不实造成张拉时砼局部压碎,甚至锚垫板压碎。在施工中根据钢筋的疏密程度,采用砼配合比粗骨料两级配的方案,碎石粒径0.5~1cm30%、1~2cm70%,充分增强了砼和易性及密实度。对砼拌合材料的误差进行控制:在误差方面,水、水泥、外加剂和干燥状态下的掺合料秤量应控制在±1%,对于粗、细骨料需要控制在±2%;投料顺序:按照细骨料、水泥、掺合料、高效减水剂的顺序投入混合料,并搅拌30s,然后加水搅拌30s,最后加入粗骨料搅拌60s,卸料;搅拌时间控制在120s~180s,砼搅拌到各种材料混合均匀,石子表面包满砂浆,并且颜色保持一致,每个投料阶段不应少于30s。采用附着式振捣器配合20 振捣棒进行振捣,控制砼的捣固时间、插捣间距,将砼内气体引出,灌注砼时既不能过捣也不能漏捣。严格按配合比施工。为防止粘模,采用模板漆作脱模剂,保证了砼表面的光滑度。采取以上措施避免了砼表面蜂窝麻面,解决了锚垫板后面砼浇筑不实现象。
3.2 为避免带角度预制梁在张拉过程中出现梁端小角度部分拉裂现象,加强小角度部分砼捣固、适当增加钢筋数量方法解决。一旦出现拉裂现象,采用环氧树脂、乙二胺、二丁脂、丙酮、砂处理,比例为:配合比10:1:1:2进行修补后,再采用黑白水泥按照试验比例(2:1)进行抹面,保证砼强度和外观颜色一致。环氧砂浆配制工艺:环氧树脂加热至60℃,加入二丁脂和丙酮拌匀,加入乙二胺拌匀,再将预热至30℃的填充料加入拌匀。
3.3 预留孔道在施工过程中漏浆,无法张拉,需要清孔。施工中采用比波纹管直径略小的塑料管与波纹管同时预埋,待砼达到80%后,将塑料管拔除,避免砼进入波纹管,造成堵塞,影响穿束。
3.4 由于征拆影响,桥下部结构无法施工,且因客专开通工期要求,必须先施工预制梁,导致预制梁在场地存放时间较长,必须采用堆载方式减少预制梁上拱。根据桥铺砼重量及预制梁顶平面面积,平均分配到每片预制梁重量进行计算,得出每片梁应承担的力。计算重量后,采用砼块堆载,在每块砼下放置连续梁施工所剩木方进行分荷的方法(如表1所示)。
①箱梁徐变上拱监测。对梁体两端支座位置及跨中采用精密水准仪配合精密水准尺进行抄平监测。通过计算进一步确定梁体的上拱,通常情况下,上拱值=两端读数值之和/2-跨中读数值。安排专人同时配备专用仪器进行监测,桥梁架设后,在靠近支座选择确定两端测量位置。
②箱梁徐变上拱控制。
1)对水灰比和水泥用量进行控制:水灰比和水泥用量作为影响徐变上拱的重要因素,通常情况下,当水灰比相同时,随水泥用量增多徐变变形逐渐变大;当水泥用量一定时,随水灰比的增大,徐变逐渐增加。因此,在施工过程中,需要对配合比进行严格的控制,选用的水泥用量和水灰比尽可能小。
2)选择骨料:在砼中,骨料的作用主要是约束水泥浆体的徐变,骨料的弹性模量和体积含量等因素决定着约束的程度,为了进一步控制砼的徐变变形,在施工过程中,选用的石灰石碎石骨料的弹性模量尽量高。
3)砼养护:通过对砼进行洒水养护,进而在一定程度上充分确保梁体的表面湿润性,进一步延长养护时间。
4)对终张拉时间进行控制:对于徐变上拱来说,根据线性徐变理论,施加预应力时梁体的弹性上拱量决定着徐变大小,通常情况下,较低的弹性模量造成的徐变上拱比较大。在这种情况下,需要对预应力张拉时间进行严格的控制,当砼强度及弹性模量符合设计要求后,再进行相应的终张拉。
5)控制张拉工艺:为了防止超张拉,进一步满足预应力徐变上拱限值的要求,需要实测预应力筋的管道摩阻,同时修正张拉应力,并施加预应力。
3.5 预制梁梁面施工时,采用橡胶锤对砼面进行3 次敲击后再进行收浆抹面,防止了砼表面细小裂纹的产生,既保证了工程质量,又解决了美观问题。
3.6 预应力施工注意事项:
①下料、穿束。利用砂轮锯切断钢绞线,同时用铁丝绑扎切割口两侧30mm 处;按照实际计算长度加100mm 余量确定下料长度;按编号分类存放钢束,搬运时支点距离控制在3m,端部悬出长度控制在1.5m。在穿束钢绞线束时,需要对孔道内的杂物进行清除处理,在待穿孔道的一端设置卷扬机,将钢丝绳利用钢丝引入孔中,并拉至另一端,穿束后需要尽快进行张拉处理。
②张拉设备及仪表。定期维护和校验张拉所用的机具设备及仪表。在下列情况下,必须对张拉千斤顶进行重新校验:张拉次数超过200 次;校正期限超过1 个月;千斤顶经过修理。油压表的精度为1.0~0.4 级,读数不大于1MPa,防振型。根据管道磨阻试验、油顶与油表检测书中公式进行计算得出实际油表读数。
③控制张拉力:
1)按照设计规定对锚下张拉控制力进行处理。2)预应力筋张拉控制力:
a.计入锚圈口摩阻损失。
b. 修正孔道摩阻损失,在张拉过程中进行调整。
c. 最大张拉控制力和规范规定值在任何情况下不得超过设计规定值。
④校核预应力筋张拉力:
采用张拉力控制预应力筋,同时以伸长值进行校核。实际伸长值与理论伸长值之间的差值控制在6%以内,否则需要暂停张拉,查明原因并采取措施进行调整,然后进行张拉。
1)采用设计值处理理论伸长值。
2)在初应力后开始量测实际伸长值ΔL,伸长值ΔL2根据量得的伸长值ΔL1 加上初应力下进行推算,即ΔL=ΔL1+ΔL2。
a.对于初应力,通常情况下,需要根据力筋长度、弯曲程度可取张拉控制应力的10%~15%。
b.推算伸长值ΔL2 :对于力筋来说,由于松紧、弯曲程度不一致,在初应力以下拉伸过程中,一方面有弹性伸长,另一方面有非弹性伸长,在这种情况下,不宜采用量测方法。
3)判断超误差的原因及采取的措施。
对于伸长值来说,过大或过小都会对预应力砼结构产生影响,通常情况下,产生超误差的原因主要包括:
a.作业人员在进行量测、读数时,存在的误差;
b.千斤项、油表故障;
c.千斤顶、油表未校验或校验过期、使用次数超过规定;
d.垫板与孔道不垂直或管道局部有灰浆;
e.孔道的摩擦损失计算与实际不符;
f.力筋材料质量不稳定;
g.力筋弹性模量与计算时的取值不一致;
h.操作方法不当,两端伸长值相差过大。
⑤断丝、滑移限制。按照施工规范要求,控制断丝、滑移量。通常情况下,出现断丝、滑移的原因主要包括:锚具、夹具、钢丝沾有油污;锚具不良;锚具与孔道不垂直;力筋材质出现问题。
⑥补偿预应力筋回缩产生的预应力损失。在施工规范容许值内控制预应力筋回缩。当回缩值比较大,并且长度较小时,在这种情况下,会对预应力筋的锚固性能产生影响,需要给予补偿。产生回缩的原因包括:锚具、夹具、钢丝沾有油污;锚具不良等。
⑦紧急处理锚固区发生的裂纹。对于锚固区来说,如果发生局部裂纹,在这种情况下,必须停止一切张拉和砼作业,查明原因并提出处理措施,然后才能复工。裂纹发生的原因主要包括:砼强度不足、加强钢筋设置不当、张拉力过大等。
⑧压浆封锚。完成终张拉后,在48h 内进行管道压浆处理。压浆时和压浆后的3d 内,梁体及环境温度不低于5℃。浆体水胶比不应超过0.34,水泥浆不得泌水,0.14MPa 压力下泌水率不得大于2.5% ;压入管道的浆体不得含未搅匀的水泥团块,终凝时间不宜大于12h。
4· 结论
后张法预应力砼箱梁的预制,经过施工技术的改进,最终解决了预制箱梁腹板、锚垫板后面砼浇筑不实、带角度预制梁在张拉过程中出现梁端小角度部分拉裂、预留孔道在施工过程中漏浆、上拱值过大、粱顶面砼表面细小裂纹、内膜拆模困难等影响预制构件质量的各种现象,最终预制的箱梁棱角分明,线条顺适,色泽一致,真正做到了内优外美。
上一个:浅谈高层建筑承台大体积混凝土施工
下一个:混凝土施工裂缝产生成因与治理对策